Bead making season is underway at last. The optimum temperature range for lamp working glass is between 65 and 80 degrees F, below that range and the glass is too chilled to melt properly, and above that range the artist tends to melt.
Spring and warmer weather arrived long ago but playing in the garden won out, the lawn needed mowing and the vegetable garden had to be planted. Now with summer here I can finally make time for playing with fire.
Below are a few photos of bead making in progress: you wrap an initial core of glass onto the steel rod and marver that into a cylinder, then add additional colors on top. Here I am using a technique to capture a small bubble of air by making a dent in the glass with a sharp steel tool, and then covering the dent with clear glass.
Seattle has a new glass museum, the Chihuly Glasshouse and garden will be an inspiring place to visit.

adding molten glass to the bead
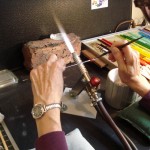
poking dents into the glass
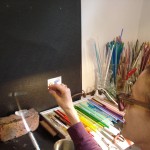
cooling the bead away from the flame
Tags: AuraSunArts, beads, bubbles, Chihuly, encasing, fire, glass, marver, melt, Seattle, spring, summer, temperature, torch
AuraSunArts, making glass beads | mary |
July 21, 2012 10:47 pm |
Comments (0)
How does one make a lampworked glass bead?
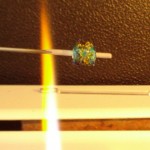
half made bead
Take a steel rod of 2 – 3 mm diameter, coated with a clay release agent, and heat up this rod in the flame. With the other hand, select a glass rod of the color needed, and introduce this slowly to the flame as well. The end of the glass rod will begin to melt, and form a blob, or “gather.” Drip this onto the rod, and wrap it around. Click on the photo for a larger view.
I usually marver the bead now, by rolling it on a flat surface until it takes a cylinder shape, and use this as my canvas to paint with more colors. I keep adding layers of color, and often finish the bead with some clear glass encasing.
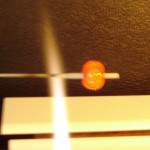
fully molten bead
The bead can be rather lumpy at this point, like a raspberry. I heat it up further until it is entirely molten, and takes on a smooth rounded shape. You must continually rotate the rod to keep the bead centered. If you wish the bead to be textured you skip this rounding. The bead can also be shaped by rolling it on a flat surface, or pressing it into a mold.
Then let it cool down until the normal colors return to the glass, and put it away in a kiln or warming thermal blanket to rest for several hours. The next day it can be taken off the rod: after a soak the clay rinses away and it twists free, the bead is complete and the rod can be re-coated with clay for the next dance.
The flame is a Minor lampworking torch with a mixture of propane and oxygen fuel. Proper ventilation and didymium safety glasses are essential. Wikipedia has several good entries relating to beadmaking and glass art.
Click on any photo here for a larger view.
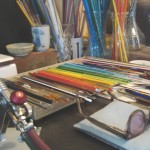
torch, glass rods, and safety glasses
Tags: beads, clay, color, didymium, encasing, glass, handmade, lampwork, marver, molten, thermal, torch
AuraSunArts, making glass beads | mary |
July 18, 2010 3:09 pm |
Comments (0)
Having some copper wire on hand,
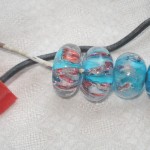
chunks of copper wire encased in glass
I thought to try incorporating some small chunks into some beads. Now if you are trying to melt copper, it is a cranky metal, and will just throw sparks as you pour on the heat with the torch, until it finally surrenders. It holds heat and conducts it, but doesn’t like to melt.
I expected the bits of copper wire to stick readily to the molten glass, but it was having none of it, only left a dent in the soft mass. Well, I flipped the bead dent side up and placed the chip of copper in the cavity with pliers and then sealed it in with clear glass encasing. Great fun! The bright copper looked fine against the turquoise glass. Turquoise and copper are mined together, a natural pair.
The molten glass behaved differently with the copper heat sink it contained, and I tried to let them cool extra slowly, but they still cracked. A grand experiment, nonetheless. Further trials with thinner gauge wire await. Click on the photo for an enlarged view.
People are sometimes puzzled when they see my jewelry.
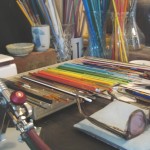
glass rods
You made the necklace, and the beads? The bead stringing they can understand, but they are sometimes shocked to hear that I made the beads themselves and ask how.
It all starts with glass rods and a torch. Here you see my work area with the many colors of glass rods arrayed on a hotplate. The red knob at lower left is part of the torch. At lower right you see the didymium safety glasses. Click on the photo to see a larger view.
Lampwork is the term used to describe working with molten glass using a small ‘lamp’ or torch. The beads are made by heating up the glass rods until liquid, and wrapping it around a steel rod coated with a release agent. After the bead is complete, the rod is removed and that leaves a hole in the bead.
Stay tuned for weekly posts about beadmaking, other artistic adventures, and the Friday Mo report!